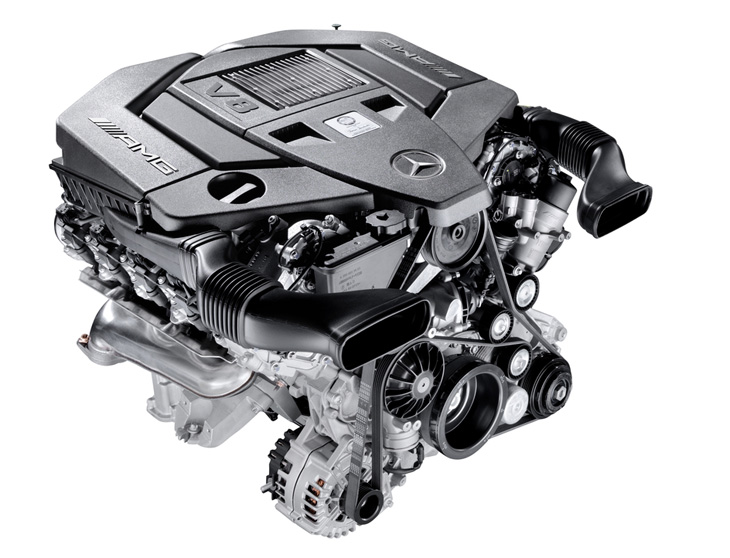
Fun With Eight, Economy With Four: New V8 Engine – Made by AMG
Mercedes-AMG has developed a new 5.5-liter V8 engine which combines powerful eight-cylinder performance with the economical fuel consumption of a four-cylinder. This unrivalled efficiency is achieved thanks to the AMG Cylinder Mana…
Mercedes-AMG has developed a new 5.5-liter V8 engine which combines powerful eight-cylinder performance with the economical fuel consumption of a four-cylinder. This unrivalled efficiency is achieved thanks to the AMG Cylinder Management cylinder shut-off system developed exclusively by Mercedes-AMG. Just like powerful, 750 hp eight-cylinder Formula 1 racing engines, cylinder shut-off is used primarily to save fuel.
Thanks to fuel savings of around 30 percent compared to the existing AMG 5.5-liter V8 engine, the high-revving naturally aspirated eight-cylinder demonstrates the great innovative strength of AMG while simultaneously demonstratiing the potential still available in naturally aspirated eight-cylinder engines.
The distinctive AMG 5.5-liter V8 engine with AMG Cylinder Management and direct fuel injection will find exclusive use in the all-new 2012 SLK55 AMG, which will celebrate its world premiere at the International Motor Show (IAA) in Frankfurt/Main in September. This means that the SLK55 AMG will remain the only roadster in its segment with an eight-cylinder engine.
Even with peak output increased by 60 hp to 415 hp and torque increased from 376 lb-ft to 398 lb-ft, the fuel consumption is about 30 percent less which places the new SLK55 AMG among the top performers in its segment.
New naturally aspirated eight-cylinder closely related to the V8 biturbo
In line with its “AMG Performance 2015” strategy, Mercedes-AMG is meeting its promise to continuously reduce both the fuel consumption and emissions of new models over the next few years with the new V8 motor – while reaching new heights with the central brand value of “Driving Performance.”
The new M152 is based on the AMG M157 5.5-liter V8 biturbo engine which first debuted on the 2011MY CL63 AMG and S63 AMG. Numerous components and systems are basically identical, e.g. the displacement, bore/stroke, distance between cylinders, ECO stop/start system and direct injection technology. Distinguishing features versus the M157 include the new intake air ducting, new cylinder heads, the modified valve drive, an adapted oil supply system and an optimized crankcase.
High performance fuel economy and output
“With the new 415 hp AMG 5.5-liter V8 engine we have once again created a real masterpiece. The M152 sets an outstanding example for efficiency, while demonstrating the creativity and expertise of our engineers, who took their inspiration from Formula 1 when developing the cylinder shut-off system. This makes the new, naturally aspirated eight-cylinder the perfect power unit for the new SLK55 AMG, which will celebrate its premiere at the International Motor Show in Frankfurt/Main in the autumn,” says Ola Källenius, Chairman of Mercedes-AMG GmbH.
“Thanks to the innovative AMG Cylinder Management system and other high-tech components, our newly developed AMG M152 naturally aspirated eight-cylinder engine achieves the fuel economy of a four-cylinder with the muscular power delivery and emotional sound experience of a V8. A sports car engine with technology taken from Formula 1 – I am convinced that the new SLK55 AMG will meet the high expectations of all sports car fans,” says Friedrich Eichler, head of powertrain development at Mercedes-AMG GmbH.
Key data* at a glance:
AMG M152 5.5-liter V8 engine
- Displacement…………5461 cc
- Bore x stroke…………98.0 x 90.5 mm (3.86 x 3.56 in.)
- Compression ratio…..12.6 : 1
- Output……………….415 hp at 6800 rpm
- Max. torque…………398 lb-ft at 4500 rpm
- Engine weight (dry)..412.4 lbs
Exclusive combination of advanced technologies
The high-tech M152 engine not only stirs emotions with its extraordinary power delivery and torque, but also thanks to a combination of advanced technologies which is unequalled anywhere in the world. No other gasoline engine features direct injection at a pressure of 2,900 psi, spray-guided combustion and piezo-injectors in conjunction with map-controlled cylinder shut-off, an all-aluminum crankcase with “spectacle” honing, four-valve technology with continuous camshaft adjustment, a high compression ratio of 12.6 : 1, an ECO stop/start system and generator management – while revving to a maximum of over 7,000 rpm. All these design features lead to high thermodynamic efficiency, which is the foundation for high fuel efficiency and low exhaust emissions.
AMG Cylinder Management
The AMG Cylinder Management cylinder shut-off system, developed completely by Mercedes-AMG, significantly improves efficiency: cylinders two, three, five and eight are cut off under partial load, which considerably lowers fuel consumption. This technology is similar to what’s used in the 750 hp V8 engines used in Formula 1. Since efficiency also plays a major role in this ultimate form of motor racing, two or four of the eight cylinders are cut off when cornering at low speed, during Safety Car laps or for pit stops.
The cylinder shut-off function is available over a wide engine speed range from 800 to 3,600 rpm if the driver has selected transmission mode “C” – Controlled Efficiency. The AMG main menu in the instrument cluster informs the driver whether cylinder shut-off is active, and whether the engine is currently running in four or eight-cylinder mode. No less than 170 lb-ft of torque is still available in four-cylinder mode – enough power to ensure plenty of acceleration in most driving situations. As soon as the driver has a need for more power and leaves the partial load range, cylinders two, three, five and eight are activated. The switch from four to eight-cylinder operation is immediate and imperceptible, leading to no loss of occupant comfort whatsoever. At an engine speed of 3,600 rpm the activation process takes no longer than 30 milliseconds.
Valves closed, fuel delivery and ignition deactivated
The cylinder shut-off system is made possible by a sophisticated engine management system, with 16 hydraulic actuators and a complex oil supply system in the cylinder head. The selectable actuators are integrated into the cylinder heads, and keep the intake and exhaust valves of cylinders two, three, five and eight closed. At the same time their fuel supply and ignition are deactivated. This not only enables the load-change losses of the four deactivated cylinders to be reduced, but also increases the efficiency of the four remaining cylinders. This is because the operating point is transferred to the higher load range. The actuators are compact and lightweight, allowing tight valve train operation and engine speeds up to 7,200 rpm.
All-aluminum crankcase with Silitec cylinder liners
The crankcase of the new AMG 5.5-liter V8 engine is made of diecast all-aluminum construction. The low (dry) engine weight of just 412.4 lbs is the result of uncompromising lightweight construction methods. The bearing covers for the main crankshaft bearings are grey cast iron, and are bolted to the crankcase as well as on the sides for high rigidity.
The piston rings are carbon-coated to minimize internal friction and optimize the wearing characteristics. Cast-in Silitec cylinder liners ensure low friction for the eight pistons. “Spectacle” honing is another measure to reduce friction and therefore fuel consumption: in this sophisticated and complex process, the cylinder liners receive their mechanical surface treatment when already bolted in place. As honing would no longer be possible with the cylinder head installed, a jig resembling a pair of spectacles is bolted to the crankcase. The cylinder liners distort as if the cylinder head were in place, and are only then given their mechanical surface treatment. As a result, any static distortion of the cylinder liners caused by tightening the cylinder head bolts can be completely eliminated.
Other measures to optimize efficiency:
- weight-optimized cast aluminum pistons with special piston skirt coating
- special ventilation holes in the crankcase
- oil pump with electrically controlled pressure stage
- separate oil pump for cylinder shut-off as a controllable, low-friction vane cell pump
- engine cooling on the particularly efficient cross-flow principle
- electronically controlled fuel pressure, fully variable and demand-related between 1,450 psi and 2,900 psi.
The forged crankshaft of high-grade 38MnS6BY steel alloy rotates in five main bearings, has eight counterweights and has been optimized with respect to torsional rigidity, inertia, low rotating masses and a long operating life. A two-mass viscous damper mounted at the front reliably eliminates vibrations. Each connecting rod journal on the crankshaft carries two forged, cracked connecting rods.
Four-valve technology with variable camshaft adjustment
Perfect charging of the combustion chambers is ensured by large intake and exhaust valves. The exhaust valves, which are subject to high thermal loads, are hollow and sodium-cooled. Four overhead camshafts operate the 32 valves via low-maintenance, low-friction cam followers. The infinitely variable camshaft adjustment within a range of 40 degrees on the intake and exhaust sides depends on the engine load and engine speed, leading to outstanding output and torque values. This also results in consistent idling at a low speed. Depending on the engine speed, valve overlap can be varied for the best possible fuel/air supply to the combustion chambers and efficient removal of the exhaust gases. The variable camshaft adjustment is carried out hydraulically via four pivoting actuators. These are electromagnetically actuated and controlled by the engine control unit. The camshafts are driven by three high-performance silent chains, which have considerable advantages in noise comfort compared to cylinder roller chains.
Controlled Efficiency stop/start function as standard
The Controlled Efficiency stop/start function further contributes to the low fuel consumption. This system is standard equipment in the new SLK55 AMG, and permanently active in the fuel economy transmission mode “C”. Once the driver brakes to a stop the V8 engine is automatically switched off. Once the brake pedal is released or the accelerator is depressed, the engine is immediately restarted and the car is able to accelerate quickly. Intelligent technology guarantees a comfortable and immediate start-up: a crankshaft sensor recognizes the direction of rotation and registers the resting position of all eight pistons. For an automatic engine start, the cylinder with the most favorable piston position receives an injection of fuel into its combustion chamber. The precise piezo-electric injectors greatly assist this process, as they make particularly fast starts possible. The M152 always starts in eight-cylinder operation.
The sophisticated engine management system ensures that the engine is only switched off if certain conditions are met. The starter battery must have sufficient charge, for example, and the engine must be at the necessary operating temperature for efficient emissions control. The same applies to the interior temperature selected by the driver: if this has not yet been reached, the engine is not switched off when the car comes to a stop. The onboard network management system makes sure that active audio, telephone or video functions are not interrupted by the stop/start function, and that the air conditioning continues to operate.
A framed “ECO” symbol in the AMG main menu shows the driver that the Page 7 Controlled Efficiency stop/start function is active. When cylinder shut-off is active, the driver is notified by the symbol “ECO4”, while “ECO8” stands for eight-cylinder operation. Should one of the above criteria prevent activation of the system, this is shown in the central display by the message “Stop/start inactive” and an “ECO” symbol with no frame. In the two more performance-oriented driving modes “S” (Sport) and “M” (Manual), the stop/start function is always deactivated. If required, the driver can also switch it off while in “C” mode as well. In this case neither a “stop/start” nor an “ECO” symbol appears.
Generator management helps to save fuel
A generator management system makes a further contribution to fuel economy: whenever the V8 engine is in overrun or when braking, kinetic energy is used to charge the battery rather than being wasted as heat in the usual way. In all other operating modes a combination of onboard network and generator management enables the generator to be kept at a low voltage. This reduces the load on the engine as well as fuel consumption when in city traffic with its frequent overrun and braking phases.
Highly efficient engine electronics for every function
All the engine functions are executed and controlled by a particularly efficient Bosch MED 17.7.3. control unit. This state-of-the-art engine computer not only controls the direct fuel injection, cylinder shut-off and variable oil supply, but also communicates with all the other onboard control units. The microprocessor has more than 30,000 different parameters and functions stored in its memory, and is able to perform up to 260 million individual operations per second. To reduce the load on the engine control unit, the eight individual ignition coils have an integral electronic module known as an ignition amplifier at each cylinder. These ensure a strong ignition spark at all engine speeds and under all load conditions. Eight high-voltage powerstages are responsible for highly precise actuation of the piezo-electric injectors.
New AMG sports exhaust system with integrated exhaust flaps
For the first time AMG is using a sports exhaust system featuring an exhaust flap on each side. This technology resolves the age-old conflict of an emotional sound during spirited driving and a more discreet engine note at low speed operation.
Each of the two rear silencers has a flap which is variably activated on a logic-controlled basis depending on the driver’s accelerator input and the engine speed. At low loads and engine speeds below 2,000 rpm the flaps remain closed. This causes the exhaust gases to cover a longer distance and flow through an additional damping element, so that the engine sound is pleasantly subdued and irritating frequencies are effectively suppressed. When the driver accelerates, the flaps open at an angle of 15, then 30 and up to 50 degrees so that some of the exhaust gases cover a shorter distance. This produces a sonorous engine note. Under full load at higher engine speeds, in performance-oriented eight-cylinder operation, both flaps are fully opened so that the occupants are able to enjoy the muscular sound typical of an AMG V8.
The twin-pipe AMG sports exhaust system with two chromed twin tailpipes on each side has a diameter of 65 millimeters from the manifolds to the pre-silencer. The diameter is reduced to 60 millimeters from the pre-silencer to the rear silencers.
Effective emissions technology with new catalytic converter boxes
The requirements for the exhaust system of the new, naturally aspirated AMG 5.5-liter V8 engine were complex – low exhaust emissions, compliance with country-specific standards and a characteristic engine sound. The SLK55 AMG meets all the requirements of the US market (LEV-III standard, On-Board Diagnosis II).
Air gap-insulated manifolds ensure a rapid catalytic converter response. For efficiency and to save space, this concept has a tandem catalytic converter housing on each side of the vehicle: adjacent to the firewall, two thin-walled ceramic substrates are grouped into each housing. This solution makes the previous, additional underbody catalytic converters unnecessary. The two ceramic substrates differ to ensure rapid and efficient emissions control: the front one is coated with palladium, while the rear one has a bimetal coating of palladium and rhodium. One lambda sensor per row of cylinders is located in front of each catalytic converter housing, and there is a lambda diagnostic sensor between each of the two thin-walled substrates.
The lambda sensors are necessary for demand-related lambda control. In all operating conditions, the constituents of the intake mixture can be precisely controlled to avoid damaging the catalytic converters. This also benefits the fuel consumption under full load, as the mixture can be leaner than in engines without this control system.
Development of the M152 began in 2008
Development of the new, naturally aspirated AMG M152 5.5-liter V8 engine began in 2008. On the basis of the M157 eight-cylinder biturbo motor, the first drafts were calculated, designed and verified by simulation. Various model and component tests were followed by numerous test series before a concept engine was finalized. The focus was on optimizing the cylinder shut-off function, with the goal of achieving the maximum fuel saving. The spray-guided direct fuel injection exclusively developed by Mercedes-Benz and also used in this new AMG V8 engine made a valuable contribution.
During the conceptual phase for the M152 the AMG engine specialists concerned themselves with fundamental packaging trials, especially concerning the placement of the selectable actuators for the cylinder shut-off function. The design of the intake and exhaust ducts was decisively influenced by the actuators, the aim being to make best possible use of the installation space in the cylinder heads to achieve the maximum output and torque yield. Configuration of the camshaft sections was also a central consideration. The challenge was not only to achieve the desired output and torque figures, but also to create a durable, dynamic valvetrain with the selectable actuators despite the high engine speeds of up to 7,200 rpm.
In addition to extensive simulations of the valve drive system, tests were Page 10 conducted on the cylinder head test bench to assess the dynamic properties of the valve drive before it was used in a finished internal combustion engine.
Perspex cylinder head for research purposes
Further component tests for the AMG Cylinder Management system were carried out using a perspex cylinder head. The AMG developers used this to analyze the complex system of oil supply ducts and selectable compensating elements in a wide range of operating conditions, e.g. when starting or at high engine speeds. This enabled extraneous influences such as air intrusion into the oil circuit to be easily identified for optimization of the system. Only after the component tests was the cylinder shut-off system tested and verified in a complete engine on dynamic simulation test benches.
The M152 presented a further challenge – verifying the performance of an engine which is strictly speaking a combination of two engines: a four-cylinder and an eight-cylinder. During the development process a large number of parameters such as injection quantities, injection times and camshaft adjustment in four and eight-cylinder operation had to be examined. The transition between the two operating modes must only occur when the camshafts are not “biting”, and the selectable actuator is not under load. The behavior of the deactivated cylinders was also continuously analyzed.
High-tech test benches for engines with over 630 hp
The Mercedes-AMG test bench facility houses nine high-tech test benches, allowing dynamic testing of engines with an output exceeding 630 hp and more than 738 lb-ft of torque. These test facilities are able to simulate any road and environmental conditions to reproduce any conceivable type of operation. Cold or hot starting, mountain passes, stop-and-go traffic or fast laps on the North Loop of the Nürburgring – the engines are required to give their utmost. Even the intake air temperatures and densities can be varied by computer control, and the engines can be alternately filled with hot and cold coolant. Fuels of different grades are also available.
Function and endurance bench testing for the highest quality
The goal of the detailed bench tests was to verify the performance of all the engine components, including the accessories. All the measurement data for the engines examined were systematically compared, and evaluated using reproducible test methods. The functioning tests were accompanied by endurance testing: to ensure the very highest quality standards over their entire operating life, the new AMG V8 engines were required to undergo 8,000 hours of endurance testing.
Extensive trials in every climatic zone on earth
At the same time the first test engines had to prove their worth in practical trials. The AMG engineers paid painstaking attention to the cylinder shut-off function, the stop/start system and the exhaust flaps. A wide range of operating conditions was chosen to ensure that the individual functions operate at a high level. Whether in the icy cold of northern Sweden, the merciless heat of Death Valley (USA), lapping the high-speed circuits in Nardo (Italy) and Papenburg or in stop-and-go traffic – the standardized test program of Mercedes-AMG includes all climatic zones and route profiles. At the same time it places the very highest demands on the day-to-day practicality, reliability and long-term durability of the new engine/transmission combination.
The SLK55 AMG test cars were taken on extended stop-and-go journeys in a number of large cities. This enabled the interaction between the different engine and transmission control units to be painstakingly examined, as well as the influence of the ambient temperature on the operating modes of the new V8 engine. Another major focus was on the further development of the control software, and its constant adaptation to the different onboard systems and environmental requirements.
Engine production – tradition of hand-built excellence
Like all other AMG engines, the new, naturally aspirated eight-cylinder is assembled by hand in the AMG engine shop commissioned in 2002. Highly-qualified technicians assemble the M152 according to the “one man, Page 12 one engine” philosophy, maintaining the very strictest quality standards. This painstaking care is attested to by the signature on the characteristic AMG engine plate.
Long tradition of powerful AMG V8 engines
Powerful eight-cylinder engines are an inseparable part of AMG’s corporate history. Established in 1967, the company immediately caused a stir with the 300 SEL 6.8 AMG which succeeded in taking second place at the 24-hour race in Spa-Francorchamps (Belgium) in 1971. The AMG racing sedan was technically based on the Mercedes-Benz 300 SEL 6.3 with the M100 V8 engine. With an engine output of 247 hp at 4,000 rpm and a top speed of 137 mph, this luxury V8 sedan with the M100 V8 engine was Germany’s fastest regular production car at the time. Classic tuning as well as an enlarged displacement from 6,330 to 6,835 cc resulted in an increase in output to 422 hp at 5500 rpm and in torque from 369 to 448 lb-ft.
Another important engine in the AMG story was the M117, its first eight-cylinder unit with four-valve technology. With a displacement of 5.6 liters, 355 hp and 376 lb-ft of torque, this V8 accelerated the 300 CE 5.6 AMG to a top speed of 188 mph in 1987. This made the coupé the fastest German car in series production, and American fans reverently christened it “The Hammer”.
The supercharged AMG 5.5-liter V8 of 2001 is another milestone in the history of AMG engine development: the M113 K delivered up to 574 hp and a torque of 590 lb-ft. The supercharged AMG 5.5-liter V8 of the SLR McLaren dating from 2003 was even more powerful – the M155 generated up to 641 hp and 605 lb-ft of torque.
2005 saw the debut of the naturally aspirated, high-revving AMG 6.3-liter V8 engine known as the M156, which developed up to 518 hp and 465 lb-ft of torque. In the new C63 AMG Coupé this eight-cylinder in combination with the Performance Package delivered 481 hp. From 2005 to the present more than 68,000 M156 engines have been produced – a record in the history of AMG. Exclusively reserved for the SLS AMG, the M159 likewise has a displacement of 6.3 liters and delivers a peak output of 563 hp, with a maximum torque of 479 lb-ft.
Closely related to the new M152, the AMG 5.5-liter V8 biturbo engine delivers between 518 hp and 563 hp depending on the model, and a maximum torque of between 518 and 664 lb-ft. The M157 is regarded as the most efficient engine in its output and displacement class. The supercharged AMG 5.5-liter V8, the AMG 6.3-liter V8 and the AMG 6.0-litre V12 biturbo were all able to win the Best Performance Engine category several times in the International Engine of the Year Awards
Mercedes-Benz Debuts Direct-Injection Engines
Direct-Injection Four and V6 Get Better Fuel Economy AND More Power
A number of 2012 Mercedes-Benz models are powered by new engines that feature direct fuel injection. The new four-cylinder and V6 get better fuel economy while producing more pulling power – an impressive feat, considering that increasing either power or fuel economy usually decreases the other.
201 Horsepower 1.8-Liter Four-Cylinder
The new-generation SLK roadster, the new C-Class coupe and the redesigned C-Class sedan are all available with a 1.8-liter in-line four-cylinder engine (201 hp, 229 lb.-ft. of torque) that’s fitted with direct fuel injection and a turbocharger. Designed with the latest four-valve-per-cylinder and double-overhead camshaft technology, the new turbo four also has two internal balance shafts to ensure it’s as smooth as a six-cylinder.
302 Horsepower 3.5-liter V6
The new-generation M-Class and R-Class sport utilities, the C- and E-Class lines and the new SLK roadster can all be equipped with a 3.5-liter V6 that produces 302 horsepower and 273 lb.-ft. of torque. Fitted with multi-spark ignition as well as direct injection, the engine is assembled in a new block with 60-degree cylinder angles, so that a balance shaft isn’t needed for smooth operation.
The previous V6 had 90-degree cylinder angles so it could be built in the same modular plant as the company’s V8s. Like its predecessor, the new engine has aluminum cylinder heads, pistons and cylinder block (with cast-in Silitec cylinders), as well as a crankshaft, connecting roads and valves made of special forged steel.
Some Direct Injection Background
While most conventional engines still use indirect port fuel injection, the world’s first gasoline engine with direct injection was the legendary 1954 Mercedes-Benz 300SL Gullwing. Since then, the company has pioneered direct injection for several high-efficiency European models, including the 2006 CLS350 CGI, powered by the world’s first gasoline engine with piezo-electric direct injection and spray-guided combustion. This advanced engine achieved 10 percent better fuel economy versus the normal V6 with port injection.
The New Direct Injection System
The fuel system on the new four-cylinder and V6 engines represents the third generation of modern Mercedes-Benz gasoline direct injection systems. First used on Mercedes-Benz diesels, the electronic fuel injectors spray gasoline directly into the combustion chambers.
In addition, the new V6 makes use of industry-leading electronics technology that features a piezo-ceramic crystalline element in each fuel injector. The piezo crystal changes shape instantly when electrical current is applied, which makes it possible to design very sensitive and precise injection systems, including the ability to program several small injections with each piston stroke. This is especially impressive, considering that engines idle around 20 strokes per second and at high speeds, run at about 200 strokes every second.
The first injection is sprayed into the combustion chamber as the piston is descending on the intake stroke. Depending on speed, load and temperature conditions, another injection or two takes place during the compression up-stroke before ignition, forming a stratified mixture.
A fourth injection can stabilize combustion if it’s needed. Among other things, this advanced spray-guided combustion process demonstrates the potential of the internal combustion engine for continued development and refinement. System pressure of the electronic direct injection is similar to mechanical injection systems – up to 2,840 psi.
Streamlined Cam Chain Drive
A new cam chain drive system on the V6 allows the hydraulic camshaft adjusters to be more than a half inch smaller in height and width. At the same time, they are now 35 percent faster, and can vary valve timing through a wider range of 40 crankshaft degrees. The crankshaft drives an intermediate shaft, and in turn, the intermediate shaft drives two short chains – one for each cylinder bank – that loop around the intake and exhaust camshaft drive sprockets.
The new chain drive results in less tension and lower chain dynamics, for even lower friction and less noise. A fourth chain drives a new variable vane-type oil pump in the bottom of the engine. At low engine speed and load, the oil pump only generates about 28 psi (or two bar) of oil pressure, and nozzles that spray cooling oil on the pistons are off. As engine speed and load increases, oil pressure goes up, and the oil spray nozzles are turned on. In this way, less energy is used when less cooling and lubrication is needed.
Multi-Spark Works with Multi-Squirt
Working together with direct injection, a rapid multi-spark ignition system on the V6 begins combustion with the first spark, but has the capability to recharge and deliver up to three more sparks within a single millisecond, creating a gas plasma with more expansion than conventional ignition.
The time lapse between sparks is adjustable, so combustion duration can actually be controlled, resulting in two percent better fuel economy, and a total of four percent improvement in combination with direct fuel injection.
Three-Phase Low-Load Cooling System
Even the cooling system is significantly refined in the new engine, beginning with a two-stage flow circuit through the cylinder head. This improved coolant flow results in better heat dissipation, despite lower coolant pressure, so that the water pump uses less engine power.
A three-phase cooling system helps the engine warm up very quickly. When the engine is first started, no coolant circulates. Then, as the engine warms up, coolant begins to circulate within the engine, but not through the radiator. Only when the coolant temperature reaches 221 degrees Fahrenheit (or 189 degrees F. under high load), coolant also circulates through the radiator. Coolant circulation through the heating system for the car’s interior is controlled separately.
Low-Friction Silicon-Aluminum Cylinder Sleeves
Mercedes-Benz was the first automaker to use innovative cast-in silicon-aluminum cylinder sleeves with a low-friction surface that allows piston-ring spring tension to be reduced by 50 percent. The efficiency payoff for low internal friction means both fuel savings and increased power.
This sleeve technology is also designed to provide exceptional block stiffness while minimizing weight. The sleeves are more than a pound lighter than conventional iron sleeves, resulting in very light components.
The Building Blocks
Assembling the new Mercedes-Benz V6 engine underscores its efficient design. An exceptionally stiff forged-steel crankshaft is bolted into a pressure-cast aluminum block, and an aluminum oil pan also contributes to block rigidity. Aluminum pistons are mounted on the connecting rods, then slid into the silicon-aluminum sleeves, which are an integral cast-in part of the block.
Connecting rods must be made in two pieces for assembly on the crankshaft, and Mercedes engines use hollow, forged steel rods that initially are made in one piece, then hydraulically “cracked,” instead of being machine-cut and reground. The irregular fracture provides a very strong, durable fit, even at high engine speeds, and shortens the production process since re-grinding isn’t necessary.
The two cylinder heads are bolted onto the block, and twin camshafts are installed in each head, with cam drive chains looping around the intake and exhaust camshaft sprockets. Double-wall exhaust piping is used to keep the exhaust air as hot as possible leading down to a catalytic converter below each cylinder bank.
2012 Mercedes-Benz R-Class Features Better Fuel Economy, More Power
R350 4MATIC Fitted with New Direct-Injection V6 Engine
The 2012 Mercedes-Benz R350 4MATIC features an all-new 3.5-liter direct-injection V6 engine (302 horsepower, 273 lb.-ft. of torque) coupled with a more fuel efficient seven speed automatic transmission. Thanks to this new powertrain the R350 4MATIC now gets significantly better fuel economy (16 city / 21 highway) while producing more power – an impressive feat, considering that increasing either power or fuel economy usually decreases the other. The R-Class is also available with a fuel-sipping BlueTEC diesel engine (210 hp, 400 lb.-ft.) that is offered in all 50 states.
New to the 2012 model year, the R-Class model line now features standard LED daytime running lights, enhancements to the interior and helpful directional lines for the standard rearview camera. A COMAND system featuring hard-drive navigation, four gigabytes of music storage, SIRIUS/HD radio, SIRIUS real-time traffic updates, Gracenote Media Database, Zagat® Survey restaurant guide guides and voice control now come as standard on all models.
More Fuel-Efficient Transmission
The 2012 R-Class line is equipped with a new 7-speed automatic transmission that has a more advanced torque converter lock-up clutch that provides even better fuel mileage, more responsive driving, quieter operation and increased durability. The new transmission is also designed to work best with a new type of low-viscosity ATF transmission fluid – colored blue instead of the usual red. Together with new planetary gears, bearings and internal seals, the “FE-ATF” fluid provides less friction and improved fuel mileage. Lower hydraulic pressure and enhanced electronic software helps provide even smoother shifting.
Details on the New V6 Engine
The new 3.5-liter V6 engine features direct fuel injection and multi-spark ignition. The V6 engine is assembled in a new block with 60-degree cylinder angles, so that a balance shaft isn’t needed for smooth operation. Like its predecessor, the new engine has aluminum cylinder heads, pistons and cylinder block (with cast-in Silitec cylinders), as well as a crankshaft, connecting roads and valves made of special forged steel.
Direct Fuel Injection
While most gasoline engines have used indirect port fuel injection in the past, the new V6 makes use of industry-leading electronics technology first used on Mercedes-Benz diesels – electronic fuel injectors that spray gasoline directly into the combustion chambers.
Featuring a piezo-ceramic crystalline element that changes shape instantly when electrical current is applied, blazingly fast piezo injectors make it possible to design very sensitive and precise injection systems, including the ability to program several small injections with each piston stroke.
The first injection is sprayed into the combustion chamber as the piston is descending on the intake stroke. Depending on speed, load and temperature conditions, another injection or two takes place during the compression up-stroke before ignition, forming a stratified mixture. A fourth injection can stabilize combustion if it’s needed.
Multi-Spark Works with Multi-Squirt
Working together with direct injection, a rapid multi-spark ignition system begins combustion with the first spark, but has the capability to recharge and deliver up to three more sparks within a single millisecond, creating a gas plasma with more expansion than conventional ignition. The time lapse between sparks is adjustable, so combustion duration can actually be controlled, resulting in two percent better fuel economy, and a total of four percent improvement in combination with direct fuel injection.
Refined Cam Chain Drive
Mounted on the ends of the intake and exhaust camshafts, the hydraulic camshaft adjusters that vary valve timing are now 35 percent faster, and with a wider range of 40 crankshaft degrees. Despite their improved performance, they’re also more than a half inch smaller in height and width.
Smaller valve timing adjusters are made possible by a new cam chain drive system, in which the crankshaft drives an intermediate shaft above the crank. In turn, the intermediate shaft drives two short chains – one for each cylinder bank – that loop around the intake and exhaust camshaft drive sprockets.
The new chain drive results in less tension and lower chain dynamics, for even lower friction and less noise. A fourth chain drives a new variable vane-type oil pump in the bottom of the engine. At low engine speed and load, the oil pump only generates about 28 psi (or two bar) of oil pressure, and nozzles that spray cooling oil on the pistons are off. As engine speed and load increases, oil pressure goes up, and the oil spray nozzles are turned on. In this way, less energy is used when less cooling and lubrication is needed.
Three-Phase, Low-Load Cooling System
Even the cooling system is significantly refined in the new engine, beginning with a two-stage flow circuit through the cylinder head. This improved coolant flow results in better heat dissipation, despite lower coolant pressure, so that the water pump uses less engine power.
A three-phase cooling system helps the engine warm up very quickly. When the engine is first started, no coolant circulates. Then, as the engine warms up, coolant begins to circulate within the engine, but not through the radiator. Only when the coolant temperature reaches 221 degrees Farenheit (or 189 degrees F. under high load), coolant also circulates through the radiator. Coolant circulation through the heating system for the car’s interior is controlled separately.
Super-Clean R350 BlueTEC Diesel Boasts 500-Mile Cruising Range
The innovative Mercedes-Benz R-Class boasts the perfect vehicle for today’s world – the fuel-sipping R350 BlueTEC diesel, which features AdBlue exhaust treatment that helps the diesel meet the most stringent 50-state emissions limits.
The R350 BlueTEC is changing consumers’ dated perceptions about diesel engines – it gets surprisingly good performance and extremely low exhaust emissions, in the process of delivering more than 20 percent better fuel economy. The roomy vehicle also boasts impressive cruising range – more than 500 miles at highway speeds, without sacrificing power.
In addition, V8-like pulling power makes the R350 BlueTEC ideal for towing when equipped with an optional 3,500-pound, Class II trailer hitch. The BlueTEC system includes an oxidation catalyst and a maintenance-free particulate filter as well as new techniques for reducing nitrogen oxide emissions – the last type of exhaust gas that’s higher in diesel vehicles than gasoline engines. The BlueTEC diesels use a NOx storage converter in combination with an SCR catalytic converter and AdBlue injection to lower NOx emissions. The AdBlue system injects an aqueous carbamide solution into the exhaust flow, which releases ammonia (NH3), reducing nitrogen oxides to harmless nitrogen and water in the downstream SCR converter.
Just the right amount of AdBlue for a given engine load and speed is injected to get the greatest reduction of nitrogen oxides. On average, only a quart of AdBlue is needed for every 600 miles driven, so its tank only needs to be refilled every 10,000 miles during normal preventive maintenance.
Telematics System
The 2012 R-Class features the ‘COMAND’ system as standard equipment with an in-dash 6disc CD/DVD changer and high-resolution 7-inch color display. The COMAND system also includes a compass function which is shown in the instrument cluster, plus a Bluetooth interface and an Aux-in connection for mobile audio devices are also integrated. The COMAND system also includes a 4 GB memory for MP3 files (Music Register), an SD memory card slot and a hard disk drive navigation system that holds various map displays.
SIRIUS real-time traffic rapidly helps guide the driver to the desired destination. Also standard is a voice-operated control system for accessing many vehicle functions, and a universal media interface to connect an external music memory or iPod to the onboard electronics and the control system. Music tracks are displayed both in the instrument cluster and the color display in the center console, and can be conveniently accessed using the keys in the multifunction steering wheel or on the dashboard. This system also enables charging of the audio device at the same time.
Passengers can also enjoy full, concert-hall surround-sound with the optional, latest-generation harman/kardon® Logic7® sound system. This high-output sound system includes a Digital Signal Processor (DSP) and Dolby Digital 5.1. Also available is an optional rear seat entertainment system with two large 8-inch screens, a DVD player and two wireless headsets for greater freedom of movement, plus a remote control.
PRE-SAFE® Gives the R-Class Reflexes to Protect Occupants
Standard on all R-Class vehicles, PRE-SAFE® is a revolutionary safety system that can actually sense an impending collision before it happens and take measures to protect occupants during those valuable seconds before impact. The PRE-SAFE system automatically tightens the front seat belts before a possible impact, and the front passenger seat moves to a position that can provide better protection. Side windows also close to provide better support for the window curtain air bags. If the system senses an impending rollover, the sunroof also closes.
The Automotive Decathlete
The R-Class combines the defining advantages of several distinct vehicles – the surefootedness of a four-wheel-drive sport utility vehicle, the performance and comfort of a sports sedan and the versatility of a luxury crossover. In comparison to other Mercedes-Benz models, the R-Class is about the same length as the flagship S-Class sedan.
With a sharp focus on design, comfort, space and performance, the R-Class is designed as a spacious, roomy vehicle with space for up to eight adults. Its standard sunroof or an optional Panorama sunroof further contributes to its openness.
The R-Class allows occupants to create their own sense of space with features such as reading lights, armrests, air vents and cup holders as well as seat adjustments for each seat and two separate-source audio plugs. This individualization is further enhanced with the optional MP3 media interface and dual-screen video entertainment system.
A Unibody Chassis Worthy of a Sports Sedan
The R-Class boasts a strong unibody platform and four-wheel independent suspension with double control arms in the front and four-link air suspension at the rear. Power-assisted rack-and-pinion steering delivers impressive on-road driving performance and comfort, and ample braking is provided by large four-wheel disc brakes, with vented discs and double-piston calipers up front.